Le phénomène de l’érosion des pièces métalliques par cavitation fait partie des risques inévitables dans certains milieux industriels. Lorsqu’un liquide s’écoule dans une atmosphère à basse pression, des bulles de gaz se forment dedans et finissent par endommager les matériaux qui l’entourent. Comment prévenir ce phénomène, qui détruit hélices, turbines, pompes centrifuges ou encore moteurs ?
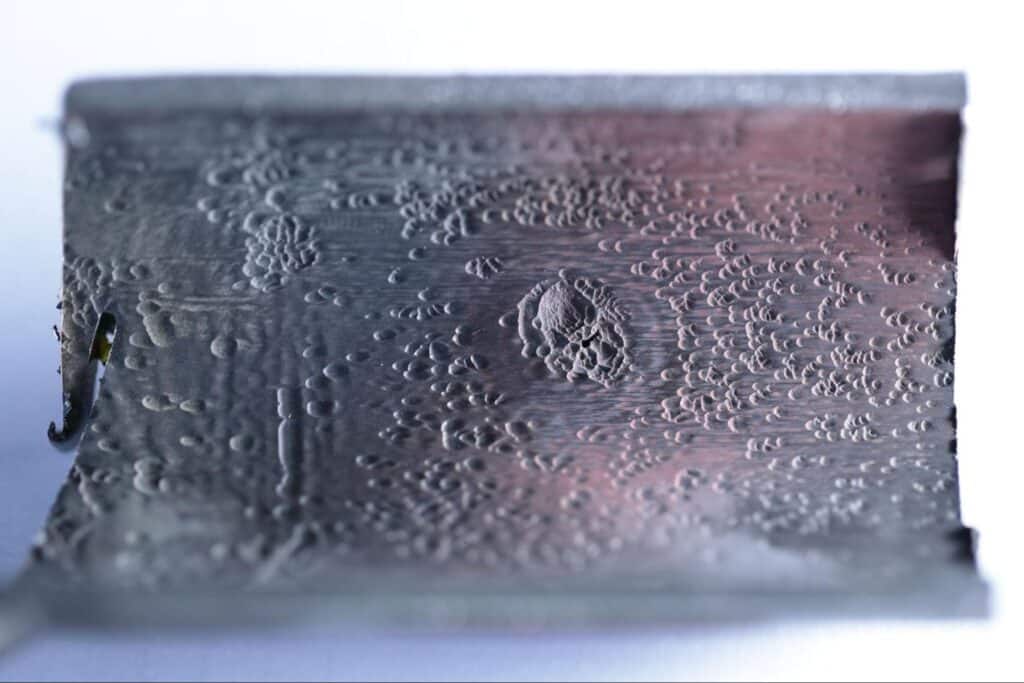
Qu’est-ce que la cavitation ?
Du latin cavus, le terme cavitation renvoie à la formation de trous. Il s’agit d’une réaction physico-chimique inévitable dans certains contextes : sous l’action d’une agitation mécanique, une baisse de pression locale peut amener un liquide à s’évaporer, même en dehors de sa température d’ébullition. Des bulles de gaz se forment et créent des ondes de choc. Ces dernières endommagent considérablement la surface des pièces métalliques à proximité.
À titre d’exemple, les moteurs diesel et les hélices marines subissent constamment ce type d’assaut : le mouvement mécanique dans un milieu liquide génère une baisse de pression dans le fluide et engendre la formation de vapeur, qui attaque les parois du moteur ou la surface métallique de l’hélice.
La cavitation reste une réaction naturelle et inévitable mais elle cause beaucoup de dégâts, notamment sur les pompes oléohydrauliques à haute pression, par exemple. Les méthodes modernes de traitement thermique des métaux permettent heureusement de mieux protéger les pièces contre ce phénomène, rallongeant ainsi leur durée de vie.
Quels sont les mécanismes de l’érosion par cavitation ?
L’érosion par cavitation est le résultat d’un mécanisme assez complexe, d’interaction entre les fluides en mouvement et les surfaces métalliques. En effet, c’est lorsque des bulles de gaz ou de vapeur se forment dans un fluide, qu’elles subissent ce qu’on nomme « un collapse brutal » sous l’effet de la pression accrue, provoquant ainsi une implosion. Cette implosion génère des ondes de choc puissantes qui altèrent la structure métallique, créent des microfissures et des décollements de matière. L’onde de choc répétée fragilise la surface et peut être aggravée par des facteurs comme la corrosion ou la présence de particules solides. Ces processus aboutissent à des dommages structurels importants dans des zones critiques comme les moteurs ou les pompes.
La nitruration pour lutter contre l’usure par cavitation
Si l’érosion par cavitation semble inévitable, il s’avère désormais possible d’agir sur les pièces métalliques pour les rendre plus résistantes. Parmi les traitements applicables pour lutter contre ce phénomène, on trouve notamment la nitruration. La pièce métallique est alors durcie par un traitement superficiel à base d’azote, qui la protège plus efficacement et plus longtemps.
Le processus de nitruration
Ce traitement superficiel de diffusion consiste à chauffer la pièce métallique en présence d’autres gaz permettant de générer une forte concentration d’azote en surface de la pièce.
Cet élément réagit alors avec le fer et provoque l’apparition de nitrures de fer, qui “recouvrent” la couche superficielle de la pièce métallique. On parle alors de couche de combinaison. En dessous se forme la couche de diffusion. L’ensemble de ces deux couches forme la couche nitrurée.
L’épaisseur de cette couche nitrurée dépend notamment du temps, de la température et de l’atmosphère dans laquelle la pièce est plongée. Cette réaction a pour effet d’améliorer nettement la dureté et la résistance de sa surface au phénomène d’érosion par cavitation. Le groupe THERMILYON propose trois procédés de nitruration : ionique, gazeuse et vide. Il est également possible de faire un traitement de post oxydation afin d’améliorer la résistance à la corrosion (THERMI®-NITROX)
Les avantages du traitement par nitruration
La nitruration des pièces métalliques prolonge grandement leur durée de vie. Ce traitement ralentit l’usure des pièces et améliore leur résistance au grippage, à la fatigue et à l’érosion par cavitation.
Le risque de déformation se voit également limité. La nitruration présente également un avantage économique certain : la pièce durant beaucoup plus longtemps, plus besoin de la réparer, de la remplacer souvent ou de veiller à son entretien permanent. De ce fait, ce traitement profite à l’ensemble de la productivité sur le long terme.
Pour certaines applications où les pièces sont réalisées en acier inoxydable, des traitements superficiels type THERMI®-SP présentent des solutions intéressantes.
Modélisation et prédiction de l’érosion par cavitation
La modélisation et la simulation CFD (Computational Fluid Dynamics) sont devenues des approches incontournables pour prédire le phénomène d’érosion par cavitation. C’est grâce à ces outils qu’il est possible d’anticiper des potentielles zones à risque sur des pièces métalliques, en analysant les flux précis et les différentes pressions locales. En parallèle de cela, des essais en laboratoire, conformes aux normes internationales, permettent de valider les prédictions numériques. Ces méthodes combinées offrent une vision complète pour prévenir l’érosion, optimiser la durée de vie des composants, mais aussi réduire les coûts de maintenance.
Le Groupe ThermiLyon dispose d’un savoir-faire reconnu en traitement thermique et nitruration pour tous types de pièces métalliques. Parlons de votre projet !