La nitruration fait partie des traitements thermiques de surface les plus courants et repose sur la diffusion d’atomes d’azote. Il s’agit d’une méthode très complète, qui possède de nombreux avantages et participe notamment à renforcer la résistance globale des pièces en acier. Elle se décline en trois variantes, qui se déroulent dans des milieux différents : la nitruration liquide, gazeuse et ionique.
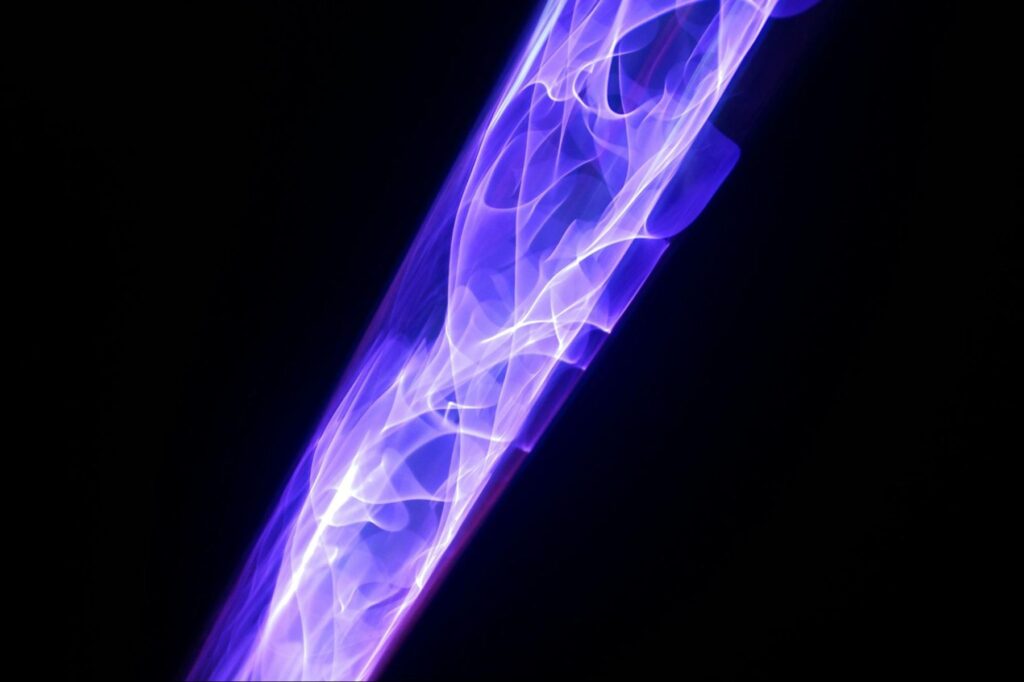
La nitruration : protéger les pièces en fabricant de l’azote atomique
Comme son nom le laisse entendre, le fonctionnement de la nitruration se base sur l’utilisation d’azote. Il s’agit d’un traitement de diffusion, au cours duquel on fabrique de l’azote qui se dépose à la surface des pièces puis diffuse à l’intérieur des pièces. Dans “la nature”, cet élément n’est présent qu’à l’échelle moléculaire (N2), trop gros pour entrer dans les interstices du métal tel que l’acier et le protéger. C’est pourquoi la nitruration a pour but de générer de l’azote atomique(N), nettement plus adapté.
Cette méthode s’emploie de plus en plus depuis quelques années car elle présente de nombreux avantages : elle se déroule dans un environnement à basse température, ce qui induit des économies d’énergie et simplifie les gammes d’usinage, améliore la résistance des pièces à l’usure, à la fatigue ou encore à l’abrasion et cause très peu de déformations au cours du traitement.
En ciblant la diffusion de l’azote et en contrôlant la profondeur et la formation de la couche nitrurée, ce procédé de traitement permet d’obtenir une couche superficielle très performante qui prolonge considérablement la durée de vie et les propriétés mécaniques des pièces métalliques, telles que les engrenages et les composants d’outils, dans des environnements exigeants, notamment dans l’industrie.
Les trois grands types de nitruration
En pratique, la nitruration peut avoir lieu dans différents milieux : liquide, gazeux ou ionique. Si le résultat de l’opération demeure similaire en termes de performances dans les trois cas, le choix de la méthode dépend avant tout des pièces à traiter, de leur géométrie mais aussi de la nature de chaque commande ou encore du budget disponible.
Nitruration liquide : la méthode des bains de sels fondus
L’un des plus anciens procédés de nitruration reste celui dit des bains de sels. Celui-ci se déroule dans un environnement liquide. La nitruration liquide consiste à chauffer des sels à une température comprise entre 500 et 600 degrés Celsius. Ces sels sont composés de cyanates(CNO), qui se décomposent ensuite en azote atomique. Ainsi, les pièces de métal plongées dans le bain de sel se “recouvrent” naturellement d’une couche nitrurée, qui protège toute leur surface.
Nitruration gazeuse
La nitruration gazeuse repose sur l’utilisation d’un gaz bien précis, l’ammoniac, NH3. Ce procédé implique de décomposer cette molécule pour former de l’azote atomique qui diffuse dans la pièce métallique. Pour ce faire, l’environnement est chauffé entre 500 et 600 degrés Celsius dans un four, généralement de forme cylindrique, type pot ou de forme cubique. Les pièces à traiter y sont disposées et le gaz actif est injecté et maintenu à température pendant un temps défini à l’avance, en fonction de la profondeur de couche souhaitée.
Cette méthode possède une variante, connue sous le nom de nitruration gazeuse basse pression. Dans ce cas précis, la pression atmosphérique est abaissée de 1 000 millibars à 450 – 500 millibars, ce qui permet d’utiliser moins d’ammoniac.
Nitruration ionique ou plasma
Le troisième cas de nitruration prend place en milieu ionique. On parle également de nitruration plasma. Cette méthode s’appuie sur la formation d’ions N+, que l’on diffuse à la surface des pièces en acier pour y faire pénétrer l’azote. En pratique, cette technique consiste à créer un plasma, assurant à la fois le décapage et en partie le chauffage des pièces. Celles-ci sont donc placées dans un four, comme dans la situation précédente et refroidies par la circulation forcée de gaz neutre à la fin du cycle.
Ce procédé est particulièrement adapté aux applications nécessitant une dureté de surface élevée et une résistance au grippage, ce qui en fait un excellent choix pour les engrenages et autres composants soumis à de fortes contraintes.
Chaque type de nitruration offre des avantages uniques et est envisagé en fonction du matériau, des propriétés souhaitées et des besoins spécifiques de l’application. Ce traitement thermochimique permet non seulement d’accroître la durabilité et les performances des pièces métalliques, mais aussi d’obtenir des avantages à long terme en termes d’intégrité mécanique et structurelle.
Choisir son procédé de nitruration
Ces trois procédés de nitruration donnent, dans les faits, des résultats tout aussi bons en termes de performances. En effet, ces trois technologies servent le même objectif : faire entrer de l’azote à la surface de pièces en acier pour les renforcer et améliorer, entre autres, leur résistance à l’usure. Ainsi, définir la méthode adaptée implique de se pencher sur chaque commande au cas par cas dans un esprit “besoin du client ».
Par exemple, dans le cas de pièces dotées d’une géométrie particulière, nécessitant un traitement partiel, la méthode ionique représente souvent la technologie la plus adaptée. Grâce à l’utilisation de caches métalliques, il s’avère possible de réaliser la couche nitrurée seulement sur les zones souhaitées à la surface de la pièce. Cependant, cette méthode impose de prendre quelques précautions : si deux pièces se touchent au cours du traitement, un arc électrique se forme entre elles et les fait fondre. De ce fait, la nitruration plasma ne peut pas convenir aux lots en vrac. Si la commande prévoit une importante quantité de pièces à traiter, en règle générale, mieux vaut privilégier la technique des bains de sel ou la nitruration gazeuse.
Par ailleurs, certains fabricants obéissent à des contraintes environnementales et d’économies d’énergie. Dans une telle configuration, mieux vaut s’orienter vers les méthodes gazeuse ou ionique, car les bains de sel doivent être constamment maintenus à une température de travail pour éviter la solidification des sels. Ils consomment donc beaucoup plus d’énergie que les deux autres procédés si l’installation n’est pas utilisée, où l’on se limite à allumer un four puis à l’éteindre une fois le traitement terminé. La nitruration liquide semble donc plus adaptée aux productions en flux continu.
De plus, cette technique implique une analyse et un suivi des bains composés d’espèces chimiques à surveiller. Même si cette technologie n’est pas soumise à REACH, régulation européenne sur l’utilisation des produits chimiques, elle produit des déchets polluants qu’il faut traiter. Pour cette raison, Thermi-Lyon a choisi d’arrêter ce procédé, que nous pratiquions depuis une cinquantaine d’années. À l’inverse, la nitruration ionique, qui se déroule sous vide, ne produit aucun déchet ni aucune pollution, il s’agit donc de la méthode la plus verte.
On distingue trois grands procédés de nitruration : liquide, gazeuse ou ionique. Ces trois méthodes fournissent d’excellents résultats et participent à améliorer la résistance des pièces à l’usure, au grippage ou encore à la fatigue. Le choix de la méthode la plus adaptée dépend en réalité de la nature des pièces à traiter. Si celles-ci n’ont besoin que d’un traitement partiel, on privilégiera une nitruration plasma, tandis que dans le cas de lots très importants, la méthode gazeuse paraît mieux adaptée. La nitruration bain de sel convient, quant à elle, très bien en cas de production à flux continu mais s’avère plus polluante et ne peut donc pas répondre aux contraintes de certains donneurs d’ordres.