Parmi les principaux procédés de revêtements des pièces métalliques, on retrouve notamment le dépôt en phase vapeur. Cette méthode permet différentes modifications des propriétés du matériau : meilleure résistance à la corrosion, à l’usure, aux frottements, changement de l’aspect visuel… Le dépôt en phase vapeur génère l’accumulation de couches minces à la surface d’une pièce et peut se faire de deux manières : chimique ou physique.
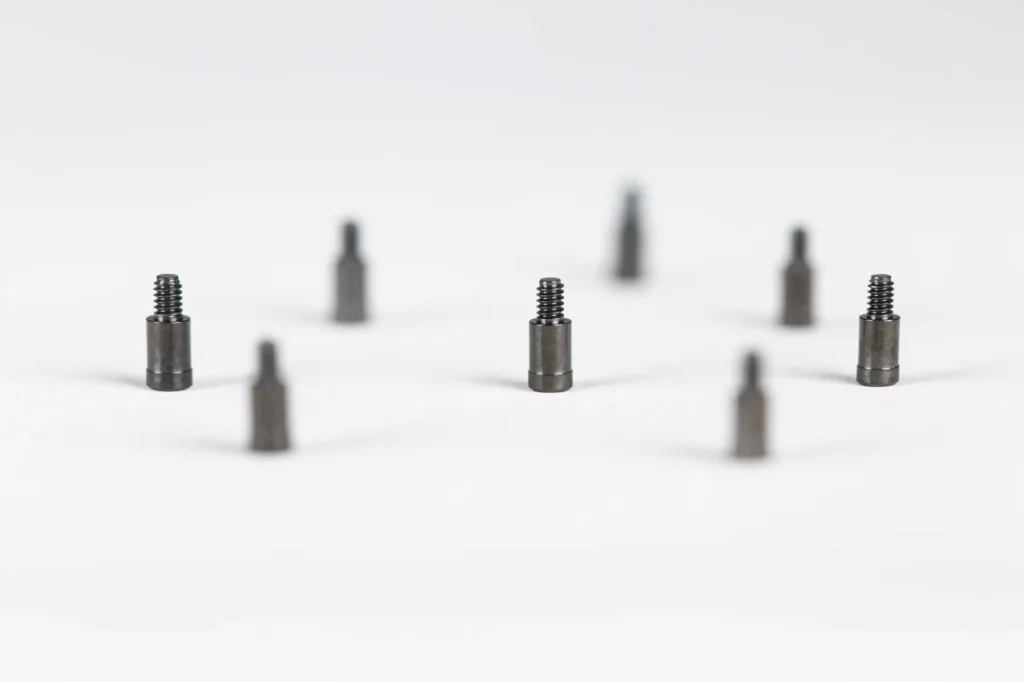
PVD, CVD : de quoi s’agit-il ?
De nos jours, la plupart des pièces métalliques industrielles subissent un traitement superficiel, indispensable pour améliorer leur usinabilité, leur résistance à la corrosion, à l’usure ou même leurs propriétés optiques ou électriques. Cette opération implique le dépôt sous vide de plusieurs couches minces de quelques nanomètres ou micromètres à la surface de la pièce. Celles-ci peuvent être appliquées de façon chimique, on parle alors de CVD, ou physique, PVD.
La CVD, Chemical Vapor Deposition, s’opère à une température comprise entre 800 et 1 000 degrés Celsius. Elle garantit un excellent résultat car elle repose sur une réaction chimique entre le substrat de base, la surface de la pièce et un composé volatil. Ces deux éléments réagissent et forment un matériau solide se déposant à la surface de la pièce. Cette technique s’avère très employée dans la production de filières d’extrusion en carbure, par exemple.
La PVD, Physical Vapor Deposition, repose sur un procédé physique. Elle se pratique à une température nettement moins élevée, allant de 200 à 450 degrés, et consiste à évaporer sous vide un matériau source pour qu’il se dépose à la surface d’une pièce. Cette méthode s’emploie notamment sur des poinçons, outils coupants et matrices.
2 critères pour choisir la bonne méthode
Pour que la réaction chimique ait lieu et que les couches adhèrent correctement à la pièce, la température de l’environnement demeure cruciale, tout comme la géométrie de la pièce à revêtir.
Température de chauffe nécessaire
Le premier critère à prendre en compte concerne la température supportée par le matériau de la pièce à travailler. Certains métaux, comme les carbures, tolèrent très bien la chaleur et représentent des candidats idéaux pour le traitement chimique, par CVD. L’avantage principal de cette méthode reste la qualité de l’adhérence du revêtement, ainsi que la rapidité du processus. D’autres à l’inverse, tels que l’aluminium, ne peuvent être traités à de trop hautes températures sous peine de se mettent à fondre. Dans ce cas, mieux vaut opter pour un procédé par PVD. Pour bien choisir son procédé de revêtement, il faut donc avant tout tenir compte de la température nécessitée par la méthode, CVD ou PVD, et de la tolérance du matériau dans de telles conditions.
Géométrie de la pièce
En plus de la température, il convient de surveiller la géométrie de la pièce. Si la méthode PVD s’applique parfaitement à la surface de nombreuses pièces métalliques, elle peut toutefois s’avérer inefficace dans certains cas. En effet, si la pièce comporte de trop petits trous, de quelques millimètres de profondeur, un traitement par PVD ne suffira pas forcément à les combler. Pour peu que le matériau de base ne supporte pas les hautes températures, impossible de recourir au CVD et l’on peut se retrouver dans une impasse. Il existe heureusement un nouveau système pour parer à ce phénomène.
Le PA-CVD, une technique hybride
Pour apporter le meilleur traitement aux pièces ne supportant pas les trop hautes températures et nécessitant un revêtement optimal, Thermi-Lyon utilise désormais le procédé du PACVD. Combinant les deux méthodes, cette technique déclenche les réactions chimiques souhaitées à des températures moins élevées. Ce système hybride rend possible le dépôt en phase vapeur entre 150 et 200 degrés de façon chimique et Thermi-Lyon l’exploite notamment pour ses revêtements Thermi DLC et Thermi-platin.
Thermi-Lyon dispose d’un savoir-faire reconnu en traitement thermique pour tous types de pièces métalliques.
Tout savoir sur le procédé CVD
Comment fonctionne le procédé CVD ?
Le procédé CVD ou « Dépôt Chimique en phase Vapeur » consiste, comme son nom l’indique, à déposer une couche mince de matériau solide sur un substrat à partir d’une réaction chimique en phase vapeur. On injecte ensuite un mélange de gaz réactifs dans le réacteur pour qu’i il interagisse avec la surface de la pièce sous des conditions très spécifiques de température et de pression. Cette méthode permet d’obtenir un revêtement uniforme, même sur des formes assez complexes.
Quels sont les domaines d’application du CVD ?
Le procédé CVD est utilisé pour le dépôt de couches minces de carbure de silicium (SiC), de nitrure de silicium (Si3N4), et de nitrure de gallium (GaN) sur les substrats dans la fabrication de matériaux pour semi-conducteurs, diodes électroluminescentes (LEDs) et lasers. Particulièrement dans le secteur de l’électronique, ces films permettent une croissance contrôlée des composants et une uniformité exceptionnelle.
En énergie solaire, on emploie le CVD pour créer des revêtements sur les cellules photovoltaïques via le dépôt chimique de silicium amorphe ou oxyde de zinc (ZnO), améliorant ainsi la conversion photovoltaïque et l’efficacité énergétique.
Le CVD offre des revêtements résistants aux conditions extrêmes, comme le carbure de tungstène, le carbone, ou le nitrure de titane (TiN), utilisés pour augmenter la durabilité des pièces mécaniques, outils de coupe, et moules dans l’environnement de l’industrie.
Ce procédé est aussi crucial dans la fabrication de matériaux fonctionnels pour les MEMS (systèmes micro-électromécaniques), comme le polysilicium et le nitrure de silicium, permettant la miniaturisation et le développement de micro-systèmes à haute performance.
Les avantages du procédé CVD
Le procédé CVD permet d’obtenir des films solides de haute pureté, essentiels pour des applications comme les semi-conducteurs et l’épitaxie. Il offre une grande flexibilité en permettant le dépôt de matériaux variés, comme le carbone, le tungstène ou le carbure de silicium, rendant ce procédé applicable à des secteurs tels que l’électronique, l’automobile et les revêtements spécialisés. Grâce à un contrôle précis des conditions de réaction gazeuse et des paramètres tels que la température et la pression, il garantit une croissance continue et homogène des films minces même sous forte pression. Le CVD permet également la formation d’alliages adaptés à des environnements extrêmes, tout en répondant aux besoins de production en grande quantité à une vitesse élevée.
Les inconvénients du procédé CVD
Malheureusement, ce processus CVD génère des sous-produits dangereux (toxiques, corrosifs, ou explosifs), ce qui demande des mesures de protection coûteuses pour la santé et l’environnement. Les procédés thermiques créent des contraintes sur les substrats, en particulier lorsque les matériaux ont des coefficients de dilatation qui sont différents. En plus, les gaz précurseurs, comme ceux utilisés dans la production de diamant ou encore de graphène, sont souvent assez coûteux, augmentant le coût global du processus.
Enfin, l’équipement nécessaire pour le CVD, notamment les réacteurs à plasma ou à filament chaud, représente un investissement très important, ce qui peux limiter l’accès à cette technologie pour les entreprises qui auraient des budgets restreints.